Process of production
After more than 24 years in the international market, at Pepperworld, we are still dedicated to the process and production of natural products. We have gathered the knowledge and experience of three generations in the agricultural field, meeting the highest international quality standards.
With our own processing plant, experienced staff and technology, we have 100% control of the process and the flexibility to respond to the market’s demands.
The best conditions for reception, storage and delivery
Pepperworld requires the best, to commercialize high quality products that respect the European norms as well as the rules of health and food safety. All our team is certified GlobalGap, IFS, BRC.
Storage of fruits and vegetables in appropriate and different cold rooms to ensure optimal conservation of each product (controlled temperature). A control at the stage of preparation in order to realize the rightness of the customer’s order in terms of product and packaging (traceability, code, date, labeling, food safety). A visual control of the global state of the goods to answer the requirements of the customers.
Our logistic platform guarantees an efficient and fast supply to our customers in Southern and Northern Europe. The responsiveness and efficiency of delivery are ensured for our customers, the buying centers of the supermarkets, wholesalers and industrialists of the European food market.
Recognized by certifications with higher levels, the Pepperworld Company has a large storage capacity in optimal conditions of conservation. Equipped with air regeneration systems that neutralize ethylene, fungus and bacteria, our company assures its customers the reception, storage and delivery of goods in the best conditions.
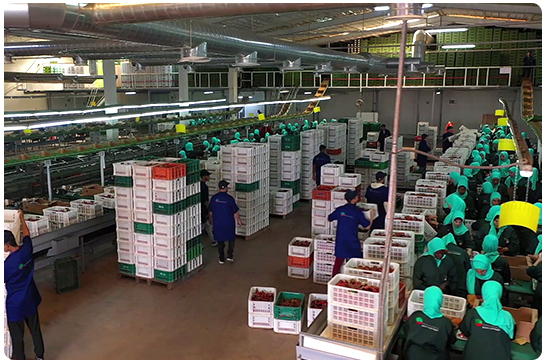
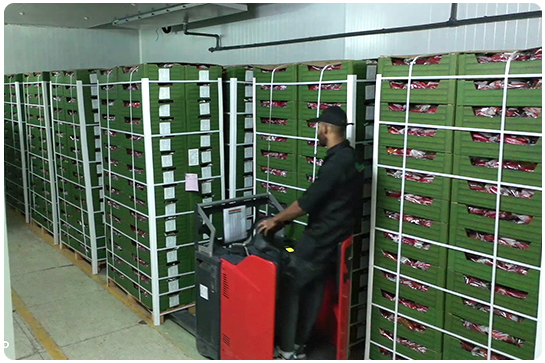
Production process in the logistic platform
The process of production in Pepperworld is as follows:
- Plantation of the plants in nursery, then passage to the greenhouse. Once the plant is mature, it is subjected to a hygiene and sanitary control. Packaging of raw materials (in batches for traceability and accompanied by a receipt that contains the information of the products and the place of their origin in case of problems) then passage to the air-conditioned storage.
- Taking of a sample in the batch by the quality department for the detection of defects. Sorting of the batches (sorting according to defects, biological characteristics, shape and size, structure, color, differences in density and foreign bodies).
- Vegetable wiping: process in which the workers wipe the vegetables.
- Packaging: Putting the vegetables in the packaging chosen by the customer.
- Labeling: Labels on the packaging that provide a set of information.
- Weighing: Following the labeling comes the procedure of weighing the packages.
- Packing: Workers pack the packages and then place them on a conveyor belt that transports them.
- Placing on conveyors: A conveyor belt that allows the package to move from the packing phase to the palletizing.
- Palletizing: Classification of the boxes according to their type while respecting the specifications.
- Strapping: Surrounding the parcels with plastic or metal bands to ensure the good maintenance during the transport.
- A quality control is applied during all these phases.
- Putting the pallets in the cold-storage rooms for a period of 3 to 4 hours.
- Passage to the loading dock.
- Calibration of measuring instruments and equipment to check whether the measurement meets predetermined requirements (weight and temperature conformity).
Our commitment to sustainable agriculture and integrated pest management implies the control of the entire production process, both in terms of fertilizers and phytosanitary monitoring due to supply chain.
This results in products of a high sanitary quality recognized by our different certifications.